R&D Story 05
Leading technology drives the evolution of electronic devices
Electronic devices are an essential part of modern life. Sunstar Engineering, with focus on craftsmanship and contemporary demands, has always developed top quality materials that assist social development and reduce environmental impact.
R&D Story 05
Leading technology drives the evolution of electronic devices
Electronic devices are an essential part of modern life. Sunstar Engineering, with focus on craftsmanship and contemporary demands, has always developed top quality materials that assist social development and reduce environmental impact.
Technology that Enables the Progress of Electronic Devices
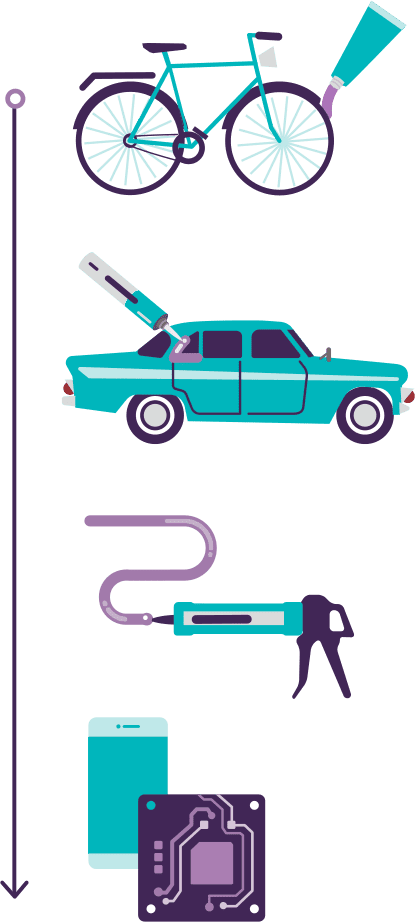
Electronic devices keep evolving to provide us with the convenience that we cannot live without. Using the telephone as an example, both its form and function have changed tremendously over the past 20 years – from being a landline to mobile, and now to a smartphone. This remarkable evolution to smaller, more sophisticated phones that are multi-functional is the fruit of advanced technology, especially for embedded components of these devices.
With its origin as a manufacturer and seller of rubber adhesives for bicycles, Sunstar now makes products in various fields, such as automotive adhesives, building sealants, and adhesives for electronic devices, using its technology and experience. Through our products, we always strive to improve daily lives of people based on their contemporary needs.
We always strive to improve daily lives of people based on their contemporary needs
"We always strive to improve daily lives of people based on their contemporary needs"
Adhesives of the Technology Era
As the use of smartphones and other highly functional electronic devices has increased, so has the demand for adhesives that protect the miniature sensitive components such as integrated circuits.
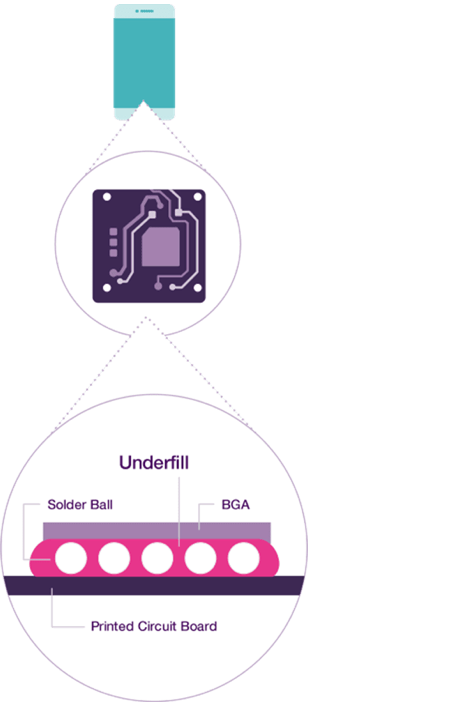
With Underfill
Without Underfill
Three Essential Properties of Underfill
There are three important properties that are highly sought after in an underfill – shock resistance or the strength against mechanical shocks,; thermal cycle resistance or the durability against temperature changes in the circuit; and reworkability or the ease of removal of the parts when repairing a defective or broken product either on the production line or the market.
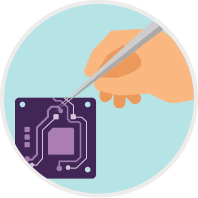
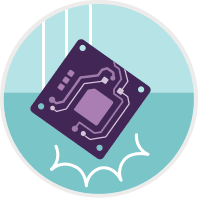
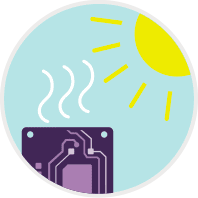
It has been a big challenge, however, to make a material that contains all these properties because they can compromise one another. To provide protection against mechanical shock, the material needs to be flexible enough to absorb the impact and to track the formation change caused by the impact. On the other hand, it needs to be rigid enough to resist expansion and contraction caused by heat. Our R&D team tackled what seems to be a complex challenge, and found answers through ceaseless trials and errors.
Creating Innovative Materials in Unprecedented Fields
Electronic devices evolve so quickly, and our R&D team often has to deal with materials that at the time have no standard criteria for strength and durability. After extensive research, they decided to develop a new underfill based on the hard yet brittle epoxy resin, and added materials to make it more shock resistant.
Creating Innovative Materials in Unprecedented Fields
Electronic devices evolve so quickly, and our R&D team often has to deal with materials that at the time have no standard criteria for strength and durability. After extensive research, they decided to develop a new underfill based on the hard yet brittle epoxy resin, and added materials to make it more shock resistant.
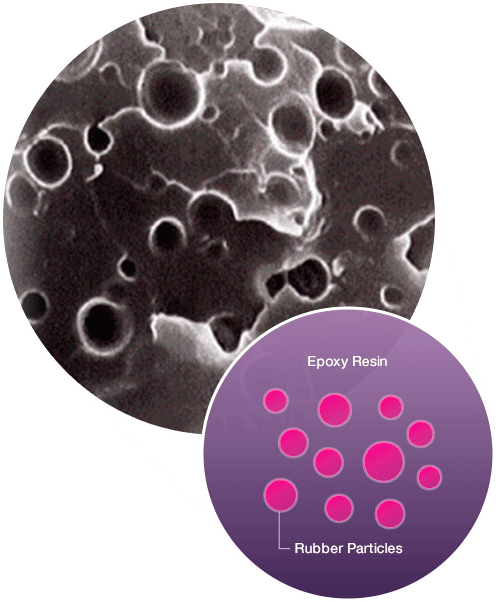
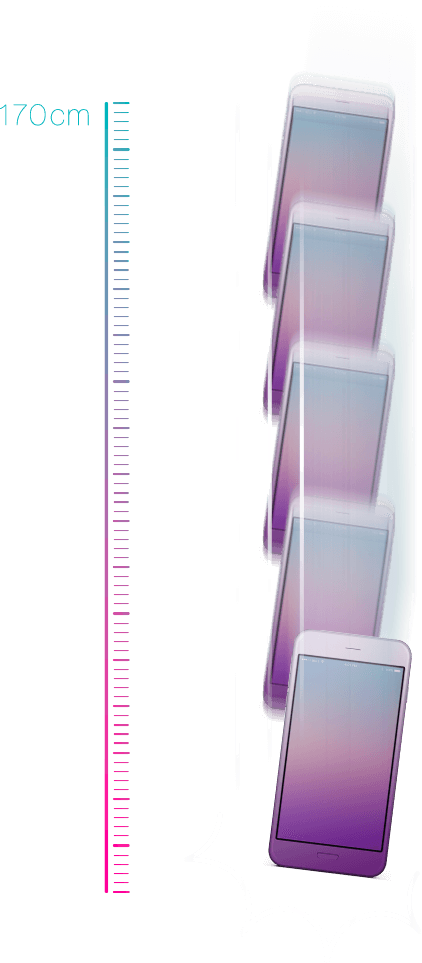
Drop Shock Test from 150 – 170 cm
A drop shock test checks the reliability of the underfill against mechanical shocks. A test device is dropped from 150 – 170 cm above the ground, to simulate an accidental drop on a concrete surface. At the initial stage, the R&D team adjusts properties of the underfill material based on the evaluation of electrical resistance and cracks from dropping a running circuit chip. When the prototype is nearly complete, they drop a functioning mobile phone repeatedly at varying angles to confirm the underfill provides a sufficient protection to the circuit.
Thermal Cycle Test: From
-40°C to 85°C
A thermal cycle test checks the reliability of the underfill against drastic temperature changes. A circuit chip with electricity running is placed in an evaluation machine, and put into an environment that changes from -40ºC to 85ºC for 1000 to 3000 cycles to evaluate its strength in protecting the circuit.
*These criteria are Sunstar R&D testing standards
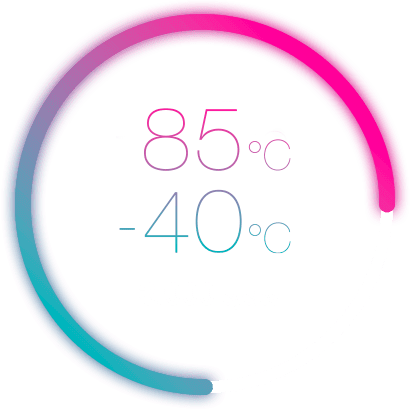
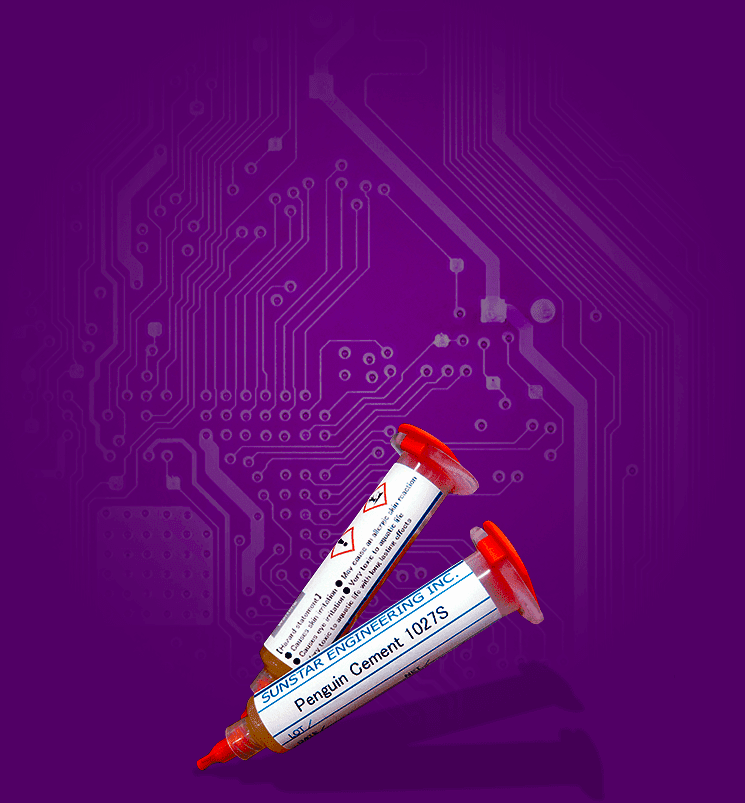
1027S Circuit Board
Underfill
After these rigorous tests, the R&D team finally developed the epoxy resin “Underfill 1027S”. It reduces shock-induced stress, withstands cracks, and is low in viscosity for efficient application onto the circuit board on the production line. This new underfill, which expanded the product life of mobile phones as well as increased manufacturing efficiency, is now used by a number of gaming and wearable devices by major brands.
Underfill With Reduced Environmental Impact
The production of electronic devices usually requires a lot of energy and may harm the environment.
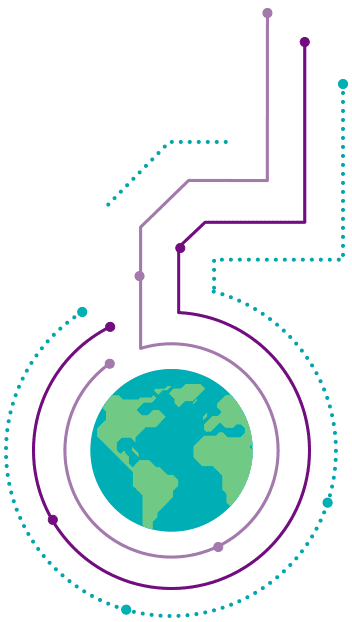
We are also contributing to the reduction of industrial waste
However, Sunstar’s underfill agents are environmentally friendly due to their outstanding manufacturing efficiency and stable under various atmospheric conditions. For example, our amine-curing agent cures at 80ºC in a few minutes – in shorter time and at a lower temperature compared to competitors’ agents – saving energy for the process.
We are also contributing to the reduction of industrial waste. Our urethane resin-based underfill is soft like rubber, which gives it a great reworkability. This means it can be easily removed from defective components on the production line or from devices sent in for repair, reducing the amount of discarded products. Sunstar’s underfill provides convenience in our lives as well as consideration for the environment.
Aiming for Excellence for the Sake of Society and the Environment
We believe that high quality underfill can reduce manufacturing energy and industrial waste. Devoted to excellence and a better future, our effort to develop superior underfill agents that are suitable for international markets continues.
Aiming for Excellence for the Sake of Society and the Environment
We believe that high quality underfill can reduce manufacturing energy and industrial waste. Devoted to excellence and a better future, our effort to develop superior underfill agents that are suitable for international markets continues.